Waste Heat to Power Technologies
Generating power from waste heat typically involves using the waste heat from boilers to create mechanical energy that then drives an electric generator. While these power cycles are well developed, new technologies are being developed that can generate electricity directly from heat, such as thermoelectric and piezoelectric generation. When considering power generation options for waste heat recovery, an important factor to keep in mind is the thermodynamic limitations on power generation at different temperatures. The efficiency of power generation is heavily dependent on the temperature of the waste heat source. In general, power generation from waste heat has been limited to only medium to high temperature waste heat sources. However, advances in alternate power cycles may increase the feasibility of generation at low temperatures. While maximum efficiency at these temperatures is lower, these systems can still be economical in recovering large quantities of energy from waste heat. The table below summarizes different power generation technologies.
Options for Heat Recovery via Power Generation
Thermal Conversion Technology | Temperature Range | Typical Sources of Waste Heat | Capital Cost ($/kW) |
Traditional Steam Cycle | Medium High | Exhaust from gas turbines, reciprocating engines, incinerators, and furnaces. | 1,500 - 2,500 |
Kalina Cycle | Low Medium | Gas turbine exhaust, boiler exhaust, cement kilns | 2,000 - 3,000 |
Organic Rankine Cycle | Low Medium | Gas turbine exhaust, boiler exhaust, heated water, cement kilns | 2,000 - 3,500 |
Thermoelectric Generation | Medium High | Not yet demonstrated in industrial applications | N/A |
Piezoelectric Generation | Low | Not yet demonstrated in industrial applications | N/A |
Thermal Photovoltaic | Medium High | Not yet demonstrated in industrial applications | N/A |
Steam Rankine Cycle
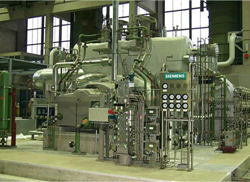
Courtesy: Siemens
The most frequently used system for power generation from waste heat involves using the heat to generate steam, which then drives a steam turbine. The traditional steam Rankine cycle is the most efficient option for waste heat recovery from exhaust streams with temperatures above about 650-700˚F [340-370˚C]. At lower waste heat temperatures, steam cycles become less cost-effective, since low-pressure steam will require bulkier equipment. Moreover, low-temperature waste heat may not provide sufficient energy to superheat the steam, which is a requirement for preventing steam condensation and erosion of the turbine blades. Therefore, low-temperature heat recovery applications are better suited for the organic Rankine Cycle or Kalina cycle, which use fluids with lower boiling point temperatures compared to steam.
Appropriate for: Waste heat recovery; medium and large CHP
Organic Rankine Cycle
The Organic Rankine Cycle (ORC) operates similar to the steam Rankine cycle, but uses an organic working fluid instead of steam. Options include silicon oil, propane, haloalkanes (e.g., "freons"), isopentane, isobutane, pxylene, and toluene, which have a lower boiling point and higher vapor pressure than water. This allows the Rankine cycle to operate with significantly lower waste heat temperatures— sometimes as low as 150˚F [66˚C]. The most appropriate temperature range for ORCs will depend on the fluid used, as fluids' thermodynamic properties will influence the efficiency of the cycle at various temperatures.
In comparison with water vapor, the fluids used in ORCs have a higher molecular mass, enabling compact designs, higher mass flow, and higher turbine efficiencies (as high as 80-85%). However, since the cycle functions at lower temperatures, the overall efficiency is only around 10-20%, depending on the temperature of the condenser and evaporator. While this efficiency is much lower than a high-temperature steam power plant (30-40%), it is important to remember that low-temperature cycles are inherently less efficient than high-temperature cycles. Limits on efficiency can be expressed according to Carnot efficiency—the maximum possible efficiency for a heat engine operating between two temperatures. A Carnot engine operating with a heat source at 300˚F [150˚C] and rejecting it at 77˚F [25˚C] is only about 30% efficient. In this light, an efficiency of 10-20% is a substantial percentage of theoretical efficiency, especially in comparison to other low-temperature options, such as piezoelectric generation, which is only 1% efficient.
ORC technology is not particularly new; at least 30 commercial plants worldwide were employing the cycle before 1984. Its applications include power generation from solar, geothermal, and waste heat sources. Waste heat recovery can be applied to a variety of low-to medium-temperature heat streams. Although the economics of ORC heat recovery need to be carefully analyzed for any given application, it will be a particularly useful option in industries that have no in-house use for additional process heat or no neighboring plants that could make economic use of the heat.
Appropriate for: Waste heat recovery
Further information:
Kalina Cycle
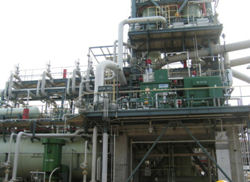
Courtesy: Raser Technologies
The Kalina cycle is a variation of the Rankine cycle, using a mixture of ammonia and water as the working fluid. A key difference between single fluid cycles and cycles that use binary fluids is the temperature profile during boiling and condensation. For single-fluid cycles (e.g., steam or organic Rankine), the temperature remains constant during boiling. As heat is transferred to the working medium (e.g., water), the water temperature slowly increases to boiling temperature, at which point the temperature remains constant until all the water has evaporated. In contrast, a binary mixture of water and ammonia (each of which has a different boiling point) will increase its temperature during evaporation. This allows better thermal matching with the waste heat source and with the cooling medium in the condenser. Consequently, these systems achieve significantly greater energy efficiency.
Appropriate for: Waste heat recovery